Descripción
Especificaciones Tecnicas De Zarandas De Separacion Solido-Liquido
Model |
Frequency
(times/min) |
Screen Area (m2) |
Process Capacity (t/h) |
Motor Power (kw) |
Dimensions
LxWxH
(mm) |
911MPEGT-936 |
1400 |
3.24 |
10-50 |
2×3 |
3840x1577x2630 |
911MPEGT-1236 |
4.32 |
15-60 |
2×3 |
3840x1877x2630 |
911MPEGT-1536 |
5.4 |
20-80 |
2×3 |
3840x2177x2630 |
911MPEGT-1836 |
6.48 |
30-100 |
2×5.8 |
3840x2477x2630 |
911MPEGT-2145 |
9.45 |
55-155 |
2×6.3 |
4740x2777x2630 |
911MPEGT-2160 |
12.6 |
90-210 |
2×8.4 |
6240x2777x2630 |
Zarandas De Separacion Solido-Liquido
El propósito de esta investigación fue determinar la ventaja de usar una malla curva (sieve bend) delante de una zaranda vibratoria o de colocar una malla de superficie curva (scalping deck ) encima sobre una zaranda vibratoria para separar partículas no deseadas cuando se efectúe una separación solido-liquido o se este drenando el medio denso de un circuito de carbón fino.
En la separación solido-liquido, el uso de la malla curva o la malla para gruesos sobre la zaranda vibratoria aumentó la capacidad del cedazo vibrante diez veces y la recuperación de carbón más fino que 0.5 mm fue mejor, sin sacrificio en el contenido de humedad del producto de sobre tamaño. En drenaje del medio denso, la malla curva o la zaranda vibratoria redujo la cantidad de magnetita retenido en el producto de la zaranda vibrante, en particular cuando el medio fue más denso como la descarga inferior de ciclones del medio denso.
La malla curva fue ligeramente superiora a la vibratoria en separación solido-liquido, pero la zaranda vibratoria fue claramente superior en drenaje del medio denso. Las ventajas adicionales de la vibratoria son costo inferior y un ahorro sustancial en espacio.
Las zarandas, en particular esos usaron para separación fina, separación solido-liquido , y la recuperación de medio denso comprende una parte significativa del costo de plantas de preparación de carbón. Su capacidad es baja en relación a requisitos del espacio; Así además del costo de estas zarandas súmese los costos de edificio. Su uso aumenta por la proporción aumentada de carbonilla en el alimento, la tendencia presente hacia remover los tamaños más finos de carbón crudo para el tratamiento separado, y la introducción del ciclón del medio denso para limpiar muy bien carbón. Así, cualquier mejora en capacidad de pantallas de zaranda contribuir a reducciones sustanciales en los costos de capital de la planta. Este objetivo llevo a la Agencia de Mines para investigar la malla curva y poco después de su desarrollo por las Minas Holandesas del Estado. En este estudio, usa de la malla curva para filtrar los tamaños finos. El trabajo presente extiende la investigación para cubrir dos otros usos importantes de la malla curva – separación solido-líquido, y drenaje del medio denso.
En el transcurso de la investigación reciente del ciclón del medio denso, fue encontrado que colocando una malla curva sobre la alimentación de una zaranda vibratoria puede servir para separar material grueso solucionando un problema del drenaje del medio. Aparentemente porque la obstrucción de las aberturas de la zaranda vibratoria fue reducida. Por consiguiente, el uso de tal cubierta para separar material grueso fue incluido.
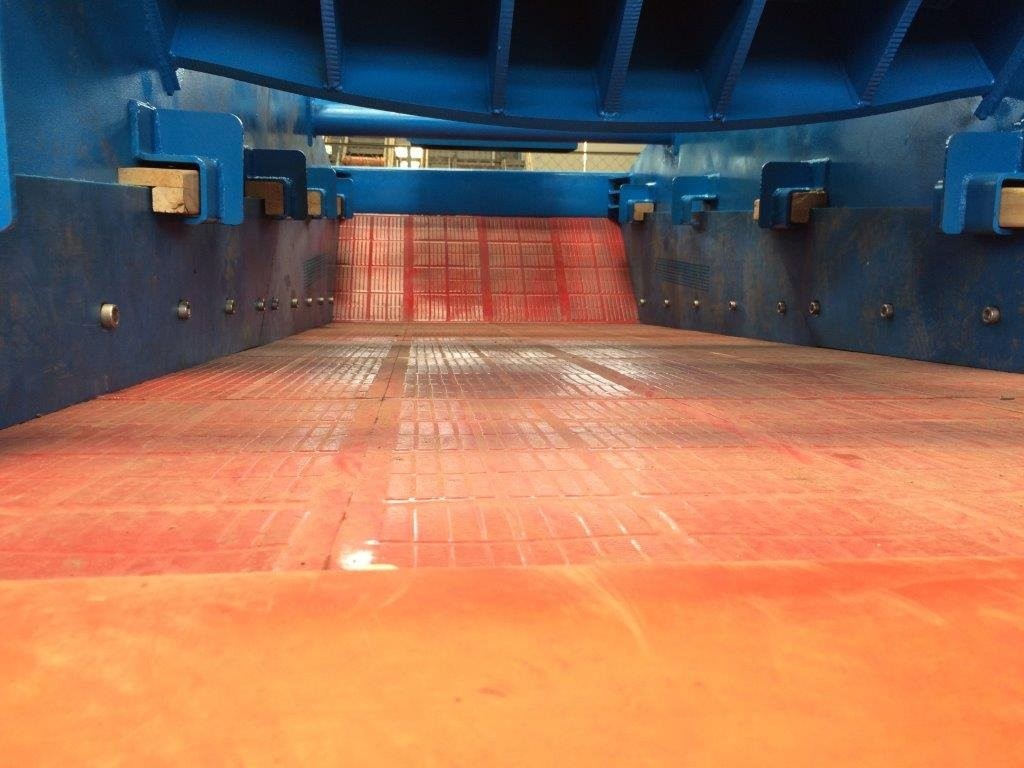
Equipo Y Procedimiento De La Prueba
El circuito experimental usado en las pruebas de drenaje es ilustrado en la siguiente figura. Una zaranda vibratoria horizontal de 26 pulgadas por 8 pies fue dividida longitudinalmente a fin de que un lado podría ser alimentado con el producto de sobre tamaño de una malla curva. El otro lado fue conectado con una malla para remover material grueso, para esto se coloca sobre la superficie de la malla curva la alimentación a la zaranda vibratoria. Si se desea, la malla curva podría quedar sin alimentación de modo que sólo la zaranda vibrante solo funcione. Así, con esta combinación, la zaranda vibrante solo, la zaranda vibratoria podría funcionar con una malla o no. Todos los pasantes de las zarandas eran recibidos en un tanque con agitación donde magnetita o un agua se agregó según se necesite para mantener densidad, luego recirculó a través del sistema por el tanque principal donde el carbón o material grueso se agregaba.
Todas las superficies de las zarandas (zaranda vibratoria, malla estacionaria, y malla colocada sobre la zaranda vibratoria) fueron de 0.5 mm. En todas las pruebas una zaranda de 4 pulgadas de ancho fue usada para retener la cantidad de material dentro de la capacidad del equipo auxiliar. El uso de la malla angosta podría exagerar el dragado que se produce en los costados de las zarandas y de esta manera se reduce su capacidad; sin embargo, la comparación de los resultados de las pruebas con la capacidad de zarandas comerciales no mostro efecto significativo. Todas las capacidades se dan por pie del ancho de la zaranda.
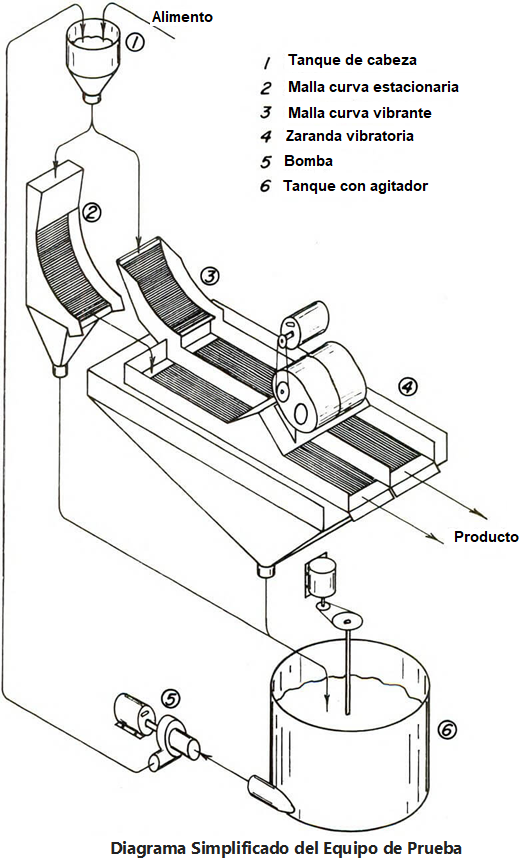
Las muestras fueron tomadas en la alimentación y la descarga de cada zaranda según la combinación elegida de tal manera que el rendimiento de cada zaranda pudiera ser estimado. Estas muestras fueron tamizadas en húmedo con malla 28, luego fueron secadas y pesadas. Las muestras fueron analizadas usando el Tubo de Davis para determinar el contenido magnético.
La magnetita usada fue un producto comercial designado Grado B y conteniendo 90% de material más fino que la malla 325. El carbón y el material grueso fueron de un tamaño de 0.5 mm a 6 mm, y se obtuvieron en el laboratorio al evaluarse una planta piloto de medios densos. Como se muestra en la siguiente tabla, estos productos contenían una alta proporción (36%) de la fracción malla 14 a malla 35. Luego fue posible efectuar pruebas de drenaje.
Typical screen analyses of coals used, percent
Size, mesh |
Dense-medium drainage |
Dewatering |
Refuse |
Washed coal |
Over 6………………….
6 to 10…………………
10 to 14……………….
14 to 20……………….
20 to 28……………….
28 to 35……………….
35 to 48……………….
48 to 65……………….
65 to 100…………….
100 to 200………….
Under 200…………. |
11
32
21
22
11
3
–
–
–
–
– |
13
34
18
23
10
2
–
–
–
–
– |
25
25
11
6
8
7
4
4
3
3
4 |
Para las pruebas de separación solido-liquido, el tanque con agitador fue eliminado del circuito. El carbón y agua fueron alimentados al tanque de cabeza y pasaron sobre las zarandas en un circuito abierto. En muchas pruebas, se tomaron muestras en varios puntos a lo largo de la zaranda. Todas las muestras fueron analizadas para determinar el contenido de humedad y distribución de tamaño. El carbón usado en estas pruebas fue un carbón lavado con la malla ¼ (6 mm), cuya distribución de tamaño se muestra en la tabla anterior.
Drenaje Del Medio Denso
Posición para retirar material grueso
Uno de los pasos de primera parte de la investigación fue determinar la influencia de la inclinación en la cual la malla para remover material grueso se colocó sobre la zaranda vibrante. Las pruebas fueron efectuadas para determinar la operación en dos ángulos de inclinación, uno con la alimentación vertical y el otro con el fin de descarga horizontal. EL carbón lavado y el material grueso, con un medio de densidad específica apropiada, fuera usada en estas pruebas. Cuando se dreno el carbón lavado, el ángulo de inclinación no tuvo importancia; Sin embargo, cuando se hizo el drenaje del material grueso, superiores fueron los resultados obtenidos cuando la descarga de la malla fue horizontal; La magnetita retenida fue reducida a la tercera parte (ver la siguiente tabla)
Influencia de la Inclinacion de la Malla para retirar Material Indesado
|
Coal or refuse feed rate, tph/ft |
Magnetite content, pounds per ton of coal |
Discharge end horizontal |
Feed end vertical |
Washed coal…………..
Refuse…………………… |
8.8
12.8 |
380
500 |
390
750 |
El medio usado con el carbón tuvo una gravedad especifica de 1.20, mientras que el rechazo (material grueso) fue 1.70. El medio más grueso se descargó con el ciclón y no dreno tan rápido como el medio que acompaño al carbón lavado. Hacer más pequeña la inclinación de la malla proveyó más tiempo de retención y por lo tanto permitió un drenaje más completo del medio. Sin embargo, con medio muy grueso, de gravedad específica 2.2 por ejemplo, el material algunas veces quedo compactado en la descarga de la malla cuando esta fue horizontal. Con un medio más grueso, mejores resultados fueron obtenido cuando la malla estuvo bastante inclinada para impedir la compactación. Por consiguiente, la malla colocada2 de esta manera para todas siguientes pruebas.
Distribución de Tamaño
Dos materiales no deseados, ambos de ¼” a 0.5 mm pero uno más grueso que el otro fueron probados bajo condiciones operativas similares. Las únicas muestras colectadas fueron el alimento y la descarga de la malla. La cantidad de magnetita retenida en la descarga cambió en proporción en la fracción de 14 a 28 mallas en el alimento; Un incremento en el porcentaje de este tamaño causó un incremento en la cantidad de magnetita retenida. La proporción de la superficie específica de estos dos materiales fue de 1.8 a 1. Así la cantidad de magnetita retenida parece estar influenciada más por la proporción de partículas cerca de la abertura (podrían obstruir la abertura) cercana que por una superficie específica. Ver la siguiente tabla.
Influencia del Tamano de Particula en el Drenaje del Medio Denso
Near-aperture size, 14- to 28-mesh, percent |
Coal or refuse feed rate, tph/ft |
Average particle size, mm |
Magnetite content, pounds per ton of refuse |
Feed |
Scalping-deck discharge |
8.8……………………….
32.2…………………….. |
10.9
7.5 |
3.54
1.99 |
5,920
6,700 |
200
820 |
Gravedad Especifica del Medio Denso
Varias combinaciones de zaranda fueron usadas en las pruebas de drenaje en las cuales la gravedad especifica del medio fue la variable principal.
La gravedad especifica vario de 1.80 a 2.20, lo cual está dentro del rango encontrado en la descarga inferior del ciclón. Estas pruebas se efectuaron a una alimentación de 7.5 tph/ft de carbón (o material grueso). Cuando solo se usó la zaranda vibratoria, la cantidad de magnetita en el producto de la zaranda incremento rápidamente al aumentar la gravedad especifica del medio. Con la malla curva o la criba para separar gruesos, el incremento fue más bajo. A una gravedad especifica de 1.85, ambas cribas fueron superiores a la zaranda vibratoria. Mejores resultados se obtuvieron cuando la malla curva o la malla para separar material grueso fue usada en combinación con la zaranda vibratoria, por ejemplo, a una gravedad especifica de 2.20, el producto de la zaranda vibratoria cuando fue usado solo con 1,900 libras de magnetita por tonelada de carbón, pero agregando la malla curva o la malla para gruesos la cantidad de magnetita fue 600 libras por tonelada. La malla de gruesos fue superior a la malla curva cuando se usó como unidad separada o cuando se usó en combinación con la zaranda vibratoria.
Los tres arreglos fueron probados con carbón lavado y un medio de gravedad especifica 1.20. la ventaja de la malla curva o la malla para material grueso no fue tan significativa con los resultados con el material grueso separado y drenado, pero la cantidad de magnetita en la descarga de la zaranda vibratoria fue reducida cerca de 50%. Cuando la producción de carbón lavado fue alta, y las cribas fueron drenadas y enjuagadas fue posible manejar mayor tonelaje de carbón lavado que el material grueso separado, entonces, la mejora por la malla curva o la de material grueso, aunque en pequeño porcentaje, podría reducir la cantidad de magnetita ingresando al circuito de recuperación del medio.
Drenaje de Carbon lavado – Gravedad Especifica del Medio 1.20
Equipment Arrangement |
Coal feed rate, tph/ft |
Magnetite content, pounds per ton of coal |
Feed |
Vibrating-screen discharge |
Vibrating screen only
Vibrating screen:
With scalping deck
With sieve bend…… |
7.5
8.0
8.0 |
1,600
1,410
1,320 |
190
100
100 |
Separacion Solido-Liquido
Capacidad de la zaranda
La primera etapa de la investigación de separación solido-liquido fue determinar la capacidad de la zaranda vibratoria sola. En estas pruebas, la razón de agua a carbón fue de 3 a 1, simulando el producto lavado (carbón) de las mesas gravimétricas. A una alimentación de 5 tph/ft de ancho de zaranda, se acumuló agua limpia en la parte superior de la cama de carbón de modo rápido. La zaranda fue sobre cargada. Con 3 tph/ft la separación solido-liquido parecía satisfactoria al inicio, pero luego de 90 minutos de operación la acumulación de agua sobre el carbón se extendió hasta la descarga de la zaranda. De manera progresiva fueron disminuyendo las obstrucciones en el área abierta de la zaranda debajo del mínimo requerido para obtener una efectiva separación solido-liquido dentro del tiempo de retención disponible.

El carbón contenía 15% del material en la fracción de tamaño malla 20 a malla 35 y un 25% adicional de material más fino que malla 35, pero fue propenso a causar obstrucción que lo que hubiera generado un carbón más grueso. Con otro carbón de un mejor tamaño, una alimentación de 3 tph/ft podría haber sido satisfactoria, una alimentación de 3 tph/ft es solo la mitad que la usada en equipo comercial pero las zarandas comerciales son de 16 a 20 pies de largo en comparación con los 8 pies de largo de la zaranda experimental.
Cuando la alimentación fue reducida a 1.5 tph/ft la separación solido0liquido satisfactoria. La acumulación de agua no se extendió al borde de la zaranda. Las muestras tomadas de la descarga de la zaranda no incrementaron la humedad después de 20 minutos de operación. Aparte del muestreo de la descarga de la zaranda, las muestras se tomaron en dos puntos a lo largo de la zaranda. Después de 10 minutos de operación, la separación solido-liquido fie completada en los primeros tres pies de longitud. La obstrucción de la malla se incrementó al aumentar la longitud de la zaranda requerida para remover el agua. Aunque el contenido de humedad no incremento después de 20 minutos. La siguiente figura muestras que el equilibrio no fue alcanzado por una hora. Todas las muestras tomadas 69 a 90 minutos tuvieron una humedad constante.
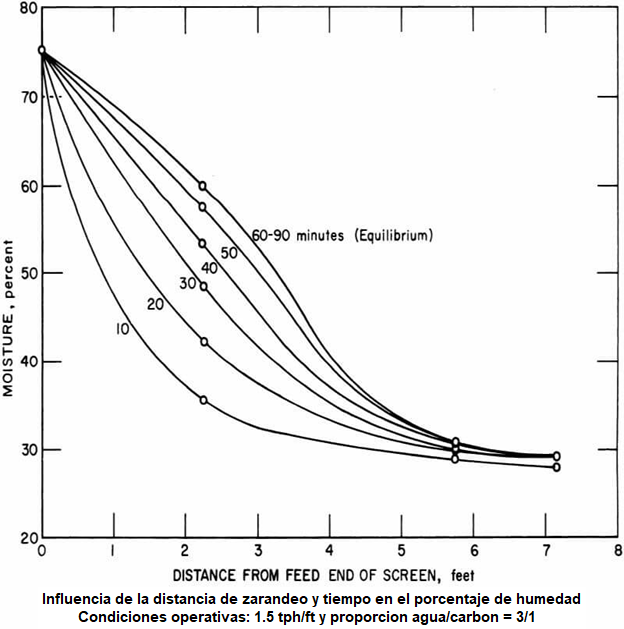
En las siguientes dos series de pruebas, la malla curva y la malla para separar gruesos fueron usadas para aliviar la carga en la zaranda vibratoria. Con ello fue posible incrementar el tonelaje de carbón que podría ser manejado con una separación solido-liquido satisfactoria. Las dos curvas mas bajas de la siguiente figura muestran que la malla curva o de gruesos con un alimento de 8 tph/ft fue sometida a separación solido-liquido completamente en los primeros dos pies de la zaranda vibratoria, y que fue alimentada con 1.5 tph/ft en los ocho pies de longitud de la zaranda vibratoria cundo solamente fue usada. Aumentado la alimentación a 16 tph/ft se tuvo un leve incremento en el contenido de humedad del producto. Este tonelaje de la combinación de cribas dio un bajo contenido de humedad en el producto final tal como fue obtenido por la zaranda vibratoria cuando se usó sola.
Con 8 o 16 tph/ft el contenido de humedad en la descarga de la zaranda vibratoria fue el mismo que usado con la malla curva o la malla de gruesos. En ambos tonelajes, la malla curva genero un producto algo mas seco que la malla para gruesos, pero la diferencia amortiguada con la zaranda vibratoria.
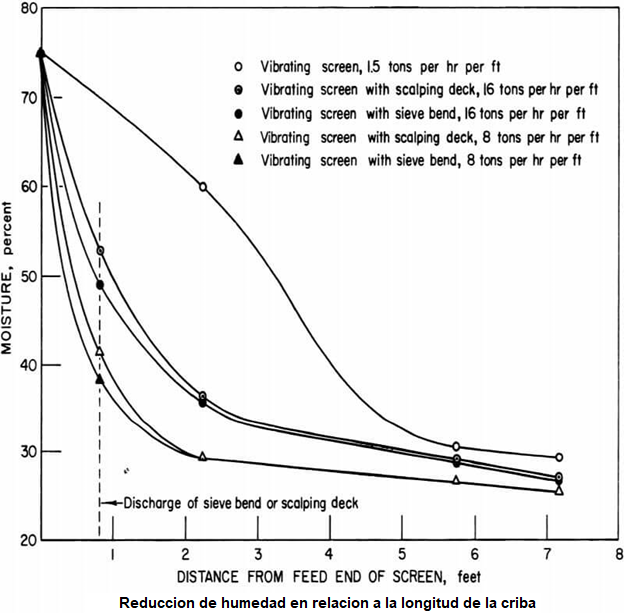
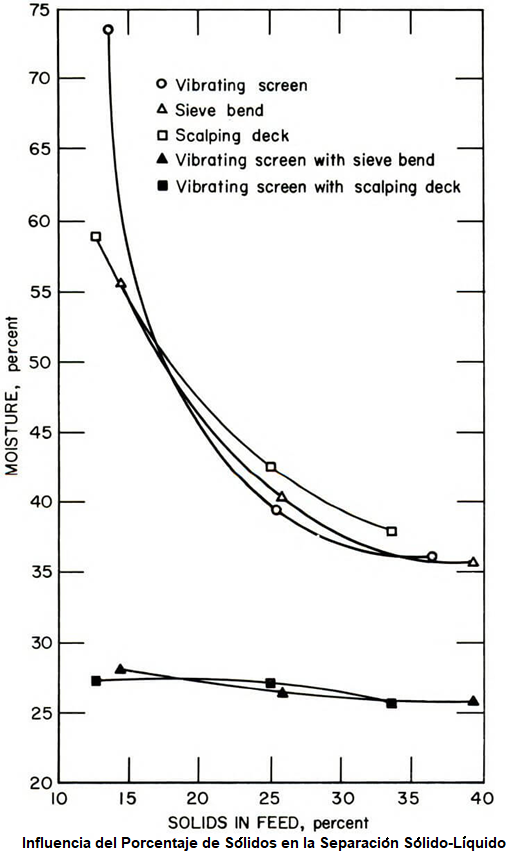
Reducción de Humedad
Debido a que las zarandas de separación solido-liquido están influenciadas por la cantidad de agua en la alimentación, una serie de pruebas se efectuaron a varias proporciones de agua a carbón usando la zaranda sola o en alguna combinación. Los resultados de estas pruebas que fueron efectuadas a 8 tph/ft se muestran en la figura anterior. Cuando la alimentación contenía 35% de sólidos, la zaranda vibratoria fue capaz de reducir la humedad a 36%. Cuando la alimentación fue mas húmeda, la zaranda vibratoria no pudo manejar la mayor cantidad de agua y el contenido de humedad en el producto se incrementó. Agregando una malla curva o una malla para separar gruesos se mejoró la separación solido líquido. Un producto con 26 a 28% de humedad fue obtenido en la zaranda vibratoria independientemente de la alimentación de agua. Con una alimentación mas húmeda la malla curva elimino mas agua que la malla para gruesos, pero la diferencia fue pequeña como para ser reflejada en el contenido de humedad del producto final.
La figura anterior no muestra la total ventaja ofrecida por la malla curva o la de material grueso porque la curva para la zaranda vibratoria no representa condiciones de equilibrio. El producto de la zaranda fue tan húmedo y la separación solido-liquido no fue satisfactoria motivando que las muestras se tomen después de unos minutos de la operación en lugar de tratar de establecer condiciones de equilibrio. En el equilibrio, la performance de la zaranda hubiera sido mala, y de ahí la mejora con cribas auxiliares hubiera sido mucho mayor.
Recuperación de Carbón Fino
La perdida de carbón fino que ocurre en las zarandas de separación solido-liquido está en función de la rapidez de la alimentación y el contenido de humedad de la alimentación. Cuando la alimentación a la zaranda vibratoria fue reducida a 1.5 tph.ft para tener condiciones de equilibrio *con una alimentación a 25% de solidos), solo 15% del carbón mas fino que malla 28 fue recuperado en la fracción retenida. Cuando la malla para gruesos fue agregada a la zaranda vibratoria y la alimentación fue 8 tph/ft, la recuperación del material mas fino que la malla 28 aumento a 37%. La malla curva fue más efectiva, se incrementó la recuperación a 49%. A 16 tph/ft, la máxima recuperación fue mejorada.
Recuperacion de Carbon Fino en la separacion Solido-Liquido
Screen arrangement |
Coal feed rate, tph/ft |
Product moisture, percent |
Recovery of 28-mesh to 0, percent |
Vibrating screen:
With sieve bend………
With scalping deck…..
With sieve bend………
With scalping deck…..
Vibrating screen only.. |
8
8
16
16
1.5 |
25
25
27
27
28 |
49
37
53
55
15 |
La siguiente figura muestra la operación a 8 tph/ft para la malla curva y la malla de gruesos con un mínimo de recuperación del carbón pasante cuando la alimentación tuvo un contenido de humedad intermedio. Esto esta de acuerdo con la observación de que la acción de separación de tamaño en la malla curva es mejor a un contenido de humedad intermedio en la alimentación. Las condiciones ideales son las peores para la recuperación de sólidos. Sobre el rango de humedad evaluado, la malla curva fue mas efectiva que la malla de gruesos para mejorar la recuperación de carbón fino. Esta superioridad puede ser atribuida al hecho que la malla curva realiza la separación a un tamaño equivalente a la mitad de la abertura. Cuando la malla curva está en vibración con la zaranda vibratoria, esta relación no es posible.
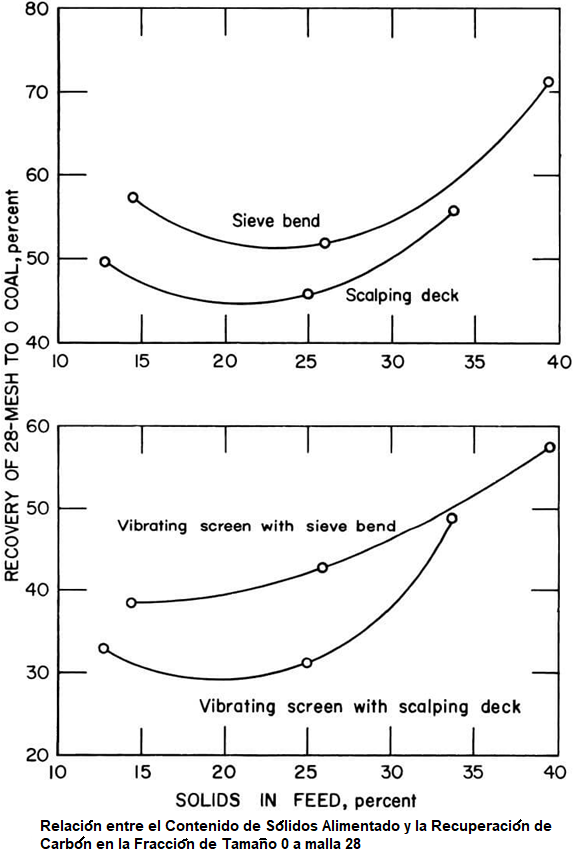
Discusion De Resultados
El mejoramiento en el drenaje del medio denso y la separación solido-líquido que ocurrió cuando la malla curva o la malla para gruesos fue usada en conjunción con la zaranda vibratoria es atribuida a dos factores. El primero es que estos equipos eliminaron lo suficiente el material cercano a la abertura y así evitar la obstrucción de la zaranda vibratoria. El grado de mejora que puede esperarse por este factor depende de la forma y tamaño del carbón. Los dos carbones usados en esta investigación tenían tendencia a tapar la abertura de la zaranda, por lo que la mejora observada fue importante.
El segundo factor responsable de la mejora cuando la malla curva o la malla para gruesos fue usada es que fue posible remover una importante fracción de líquido con lo cual se alivio la carga sobre la zaranda vibratoria. Para la mayoría de las condiciones usadas en las pruebas, estos equipos auxiliares removieron tanto liquido como la zaranda vibratoria. Este factor es independiente del tamaño del carbón.
Aunque la malla para gruesos fue algo superior a la malla curva en el drenaje del medio denso, el balance indica que la performance de ambas fue similar. La malla para separar gruesos ofrece la ventaja de requerir menos espacio, lo cual es a veces un factor critico en las instalaciones de plantas existentes. También es menos costoso porque no requiere un espacio cerrado o un sistema de tuberías. La vida y el mantenimiento de la malla son factores importantes, pero ellos no pueden ser evaluados en una investigación de laboratorio porque el tiempo de operación es corto.