Planos De Filtros De Discos
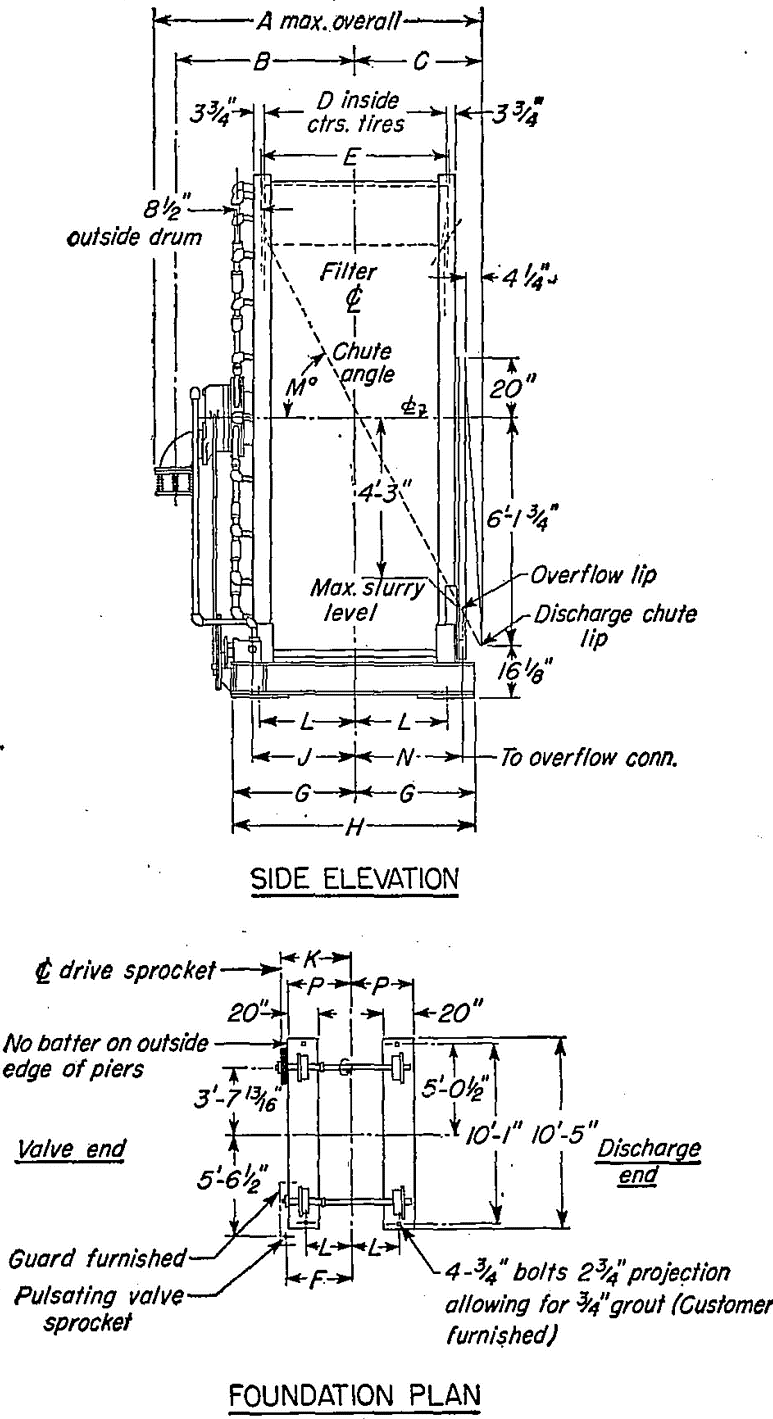
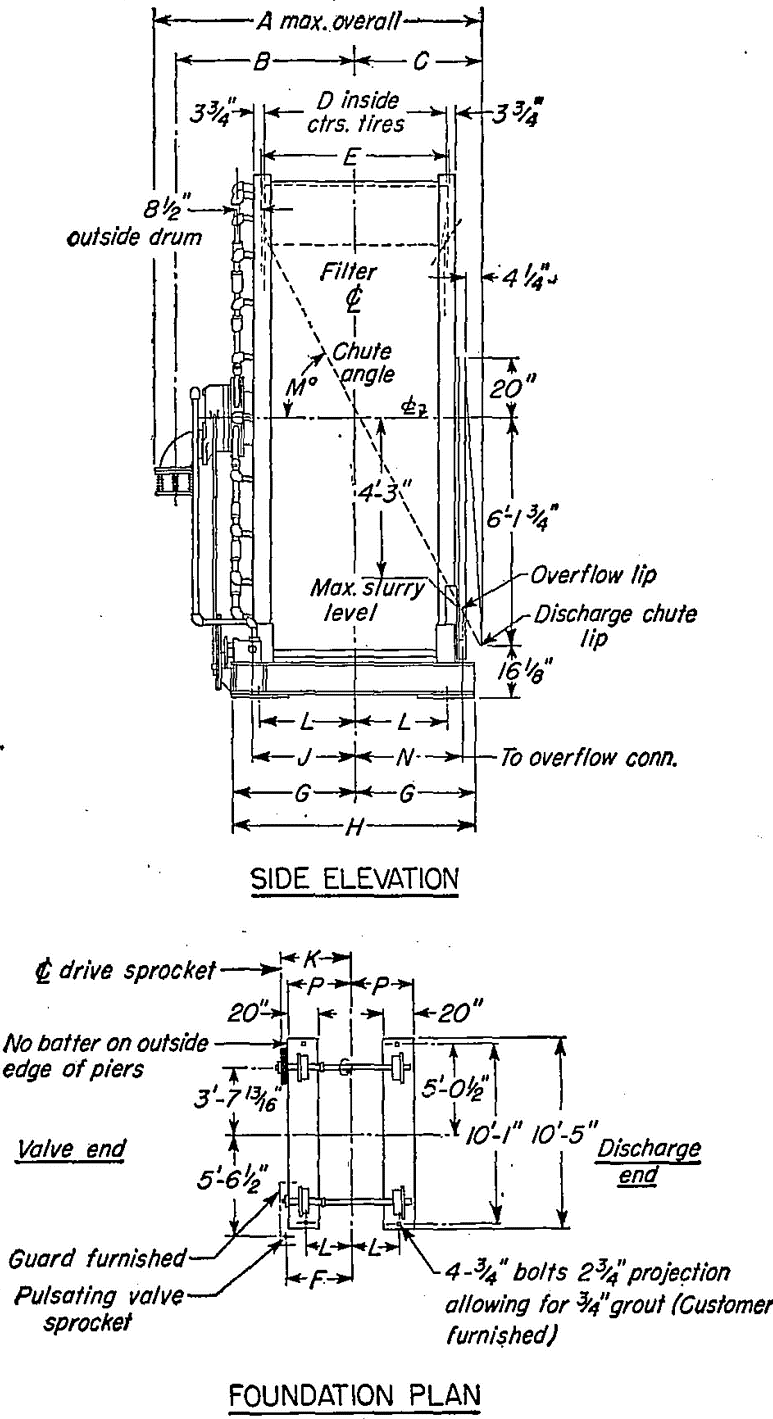
El filtro de discos es una construcción solida con cada sector esta diseñado de tal manera que pueda ser removido separadamente de otras partes del disco.
El eje central es de servicio pesado y se mueve apoyado en rodamientos, y lleva un número determinado de discos, y todo el conjunto esta montado en un tanque de hacer el cual es soportado por una estructura de acero.
El tanque tiene divisores para la descarga del queque, y puede ser dividid en uno o más compartimientos para trabajar pulpas separadas.
Dibujos De Filtros De Discos Rotatorios
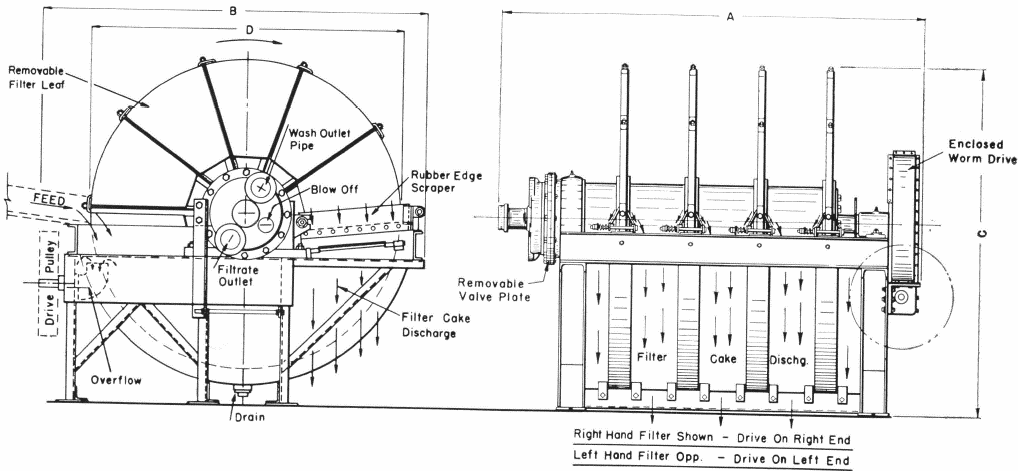
El filtro es rotado por medio de un mecanismo mecánico que puede moverse con una faja V o puede ser conectado a un reductor de velocidad.
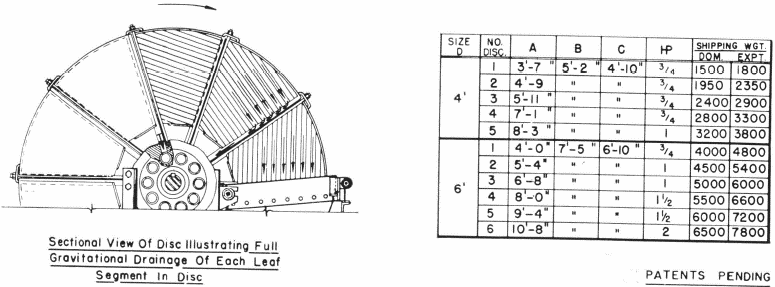
Conectores de hierro fundido están conectados al eje central, un disco, y los respectivos sectores están conectados a estos conectores con una conexión de drenaje, la cual tienen grampas para su fácil remoción. Los sectores son de madera con canales de drenaje diagonales.
El filtro de discos es una alternativa al Filtro de Tambor Rotativo y tiene la ventaja de filtrar dos o más productos simultáneamente con una sola unidad.
Consiste en un determinado numero de discos girando en un tanque y movidos por un solo eje. Los discos están divididos en segmentos o sectores y están cubiertos con un medio filtrante y están conectados con un apropiado sistema de válvulas a un sistema de vacío, causando que los sectores se encuentren bajo succión en el momento adecuado. El filtrado drena por gravedad a través de las ranuras o canales que se encuentran sobre el disco, dirigiéndose hacia un tubo de drenaje antes de descargar el queque.
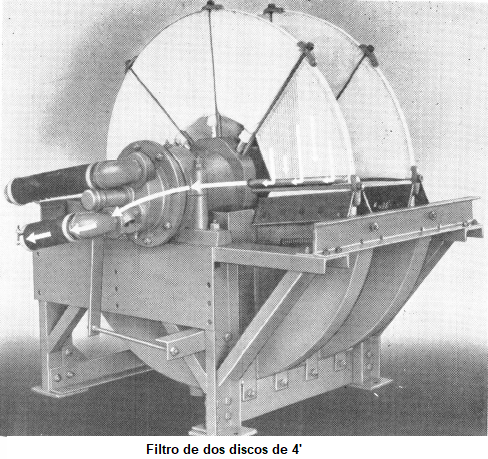
La capacidad de un filtro depende largamente de la naturaleza del material a ser filtrado, particularmente de la cantidad de material fino y lamas, y también del porcentaje de sólidos. Seguidamente se muestran capacidad promedio de un filtro de discos.
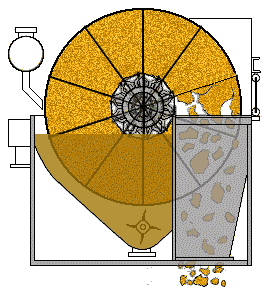
Concentrados de cobre de flotación:
150 a 300 lbs. por ft2 por 24 hr
Concentrados de plomo y zinc por flotación:
300 a 630 lbs. por ft2 por 24 hr
Relaves de cianuración:
300 a 600 lbs. por ft2 por 24 hr
Concentrados de carbon por flotacion:
1500 lbs. por ft2 por 24 hr
Barita:
3000 lbs. por ft² por 24 hr
La información anterior indica la variación en la capacidad de filtración, dependiendo del tipo de material. Las pruebas de filtración de laboratorio deben siempre efectuarse para determinar la rapidez de filtración de un material en particular. El tamaño del filtro para un determinado tonelaje, la velocidad optima, la cantidad de humedad a ser obtenida en el queque, y el tamaño del equipo de vacío requerido para el proceso.
Capacidad De Un Filtro De Discos
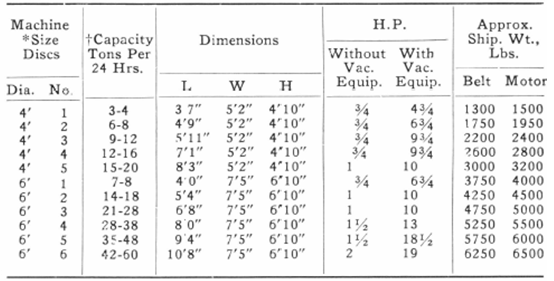
Variables Operatorias Del Filtro De Discos Rotatorio
La producción del filtro de discos depende del balance de cuatro variables, densidad de la alimentación, velocidad de los discos, condición d ellos sectores de los discos y las pulgadas de vacío (el vacío es medido en pulgadas e indica el vacío para levantar una columna de mercurio). La densidad esta controlada por la fuente de donde vienen la alimentación (espesador, tanque de retención).
La función del tanque de retención es básicamente proveer un almacenamiento de la pulpa que se alimentara al filtro. Depende del tipo de equipo disponible y de facilidad de filtrar un material.
El problema es suele encontrarse es cuánta agua se encuentra dentro del circuito sin posibilidad de drenaje. Esta situación puede alterarse si el sello de la bomba tiene fugas de agua dentro del circuito o si la alimentación al tanque tiene una densidad muy baja. Esto quiere decir que hay mas agua en el concentrado de lo que puede remover el filtro/ si hay dificultad para filtrar un concentrado el filtro deberá operar más de la cuenta. El exceso de agua por fugas en el sello de la bomba o una baja densidad indica que el filtro no seria efectivo para remover el agua del concentrado. El concentrado que puede ser retornado al tanque por una línea de rebose reducirá la capacidad de almacenamiento del tanque.
La corrección de estos problemas requiere de un buen balance de cuatro variables operativas. Conocer el balance de las variables requiere saber la forma que opera el filtro para filtrar el material. Cuando el concentrado es bombeado puede tener una baja densidad. Una determinada cantidad del concentrado con un volumen adecuado de pulpa. Los sectores de los discos reciben la pulpa cuando se aplica un vacío, y este vacío solo ejerce un efecto sobre las partículas de concentrado ubicadas a cierta distancia de los sectores del disco. El efecto del vacío es menos significativo cuando hay una mayor distancia de algunas partículas. Cunado se filtra el material, la densidad disminuye e en periodo corto de tiempo debido a que gran cantidad de partículas puede ser fácilmente levantadas. El tamaño de la partícula también influye en la capacidad del filtrado. Partículas más grandes presentan una mayor acción sobre el vacío. Considerando que hay partículas grandes y pequeñas en suspensión, la resistencia al movimiento es pequeña. Esto hace que las partículas más grandes se puedan mover más fácilmente ya que el vacío ejerce un mejor efecto sobre ellas.
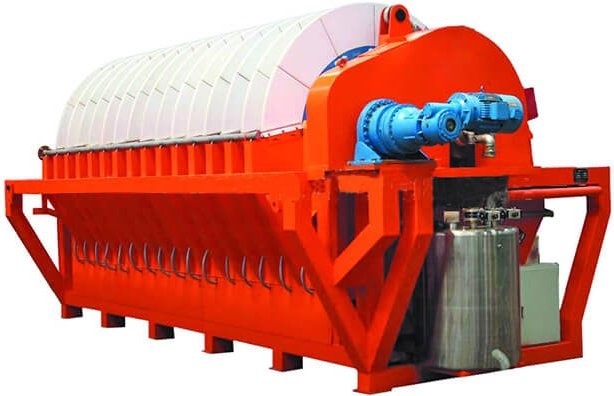
A medida que la densidad desciende, la distancia entre las partículas se vuelve mayor y la carga del filtro decrece. Esto es debido al tiempo que el sector del filtro está bajo la pulpa no es lo suficientemente largo para jalar el concentrado sobre el sector del filtro.
Después de variación inicial en la caída de densidad, la tasa de disminución se nivelará en una tasa mucho más lenta. Esto es debido a que todo el material grueso siendo sacado de la pulpa dejando sólo los finos. El material fino también causará problemas debido a que tapa la tela filtrante. El material fino se interpondrá entre el tejido en la tela de filtrar, bloqueando la abertura. Esto impedirá al vacío actuar sobre el concentrado. Esta es la razón por la que algunas minas prefieren a los operadores usando el disco a través de agua limpio o lavándolos con una manguera antes de llegar al punto abajo. Esto es para limpiar la tela lo cual ayudará a mantener su eficiencia filtrante.
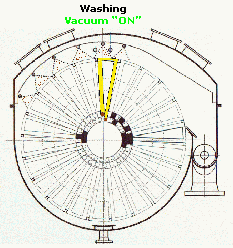
Se debe repasar las cuatro variables otra vez, la DENSIDAD, RPM del disco, PRESIÓN de VACÍO, y CONDICIÓN del SECTOR, justamente intercambiamos opiniones cómo la densidad afecta a los filtros. La longitud de tiempo que los sectores de los filtros permanecen en la pulpa tiene mucha importancia. Hay una velocidad variable en filtros que es muy efectivo de controlarse en los filtros. Si el disco es el que aumento la velocidad, el queque, el cual es el concentrado que está en el sector, será más delgado como el tiempo captación en la pulpa es menor, la cantidad de humedad en el concentrado filtrado puede cambiar. Esto dependerá de la calidad de secado del concentrado. El queque más delgado puede desecarse más fácilmente si la cantidad de partículas gruesas en el concentrado es todavía alta. Por el mayor material habrá espacios menudos entre cada uno de ellos. Esto da a la humedad la ruta a tomar durante la porción de secado en el ciclo de vacío. El material fino se compactará a sí mismo bastante bien para formar un sello impidiendo el agua pase a través de la tela.
Por otra parte, un disco moviéndose más lentamente puede generar un queque más grande, pero puede ser incapaz de secarlo debido al material más fino, cuando esto ocurre puede ser necesario balancear la tercera variable, la presión de vacío. En la mayoría de los casos habrá dos líneas separadas de vacío entrando en el filtro. Uno es el vacío de succión o levantamiento, y el el otro es el vacío de secado. Si usted controla la cantidad de vacío que está siendo usado en el ciclo de levantamiento, se controlará el espesor del queque en el sector del filtro.
El vacío durante el secado no puede recibir el beneficio del vacío adicional que no fue usado durante el ciclo de levantamiento Esto resulta en un concentrado más seco. Es importante balancear el tonelaje y el porcentaje de humedad para obtener el mejor resultado posible.
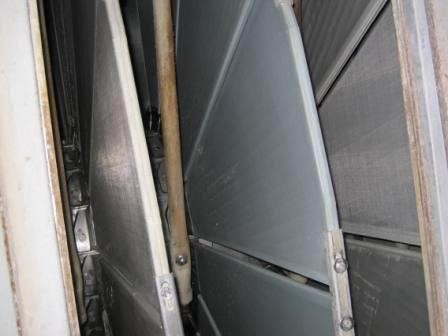
La última variable es la condición de los sectores del filtro, con ésta que hay tres áreas de interés para el operador. El SELLO, la TELA, y la INSTALACIÓN del sector. El sector y la tela tienen otros nombres como la HOJA del SECTOR o la BOLSA del FILTRO. La hoja del sector misma puede estar construida de metal, madera, neopreno. Cada uno tiene sus puntos buenos y malos.
Para el operador, sin embargo, el área principal de interés sea el método de colocar la tela filtrante. Estas bolsas tienen que cambiarse cada vez que están muy usadas y desarrollan huecos. Si la bolsa se vuelve agujereado, el vacío se caerá. No sólo en esa hoja, sino también en todos los demás que comparten el punto de distribución del vacío. El concentrado que es jalado a través del hueco y en el equipo, por el vacío se provocará una gran cantidad de desgaste adicional a que el equipo. Todo esto significa que el operador debe mantener una buena condición del filtro. Parte del trabajo es asegurar que cualquier sector agujereado es quitado y reparado. Luego hay que colocarlos en los filtros correctamente.
Donde el sector del filtro se junta con el tubo de distribución de vacío hay un SELLO, un empaque. Este empaque tendrá que ser comprobado para asegurar que no está dañado para impedir una fuga de vacío. Si ese sello falla, la falta resultante de vacío afectará la actuación de los sectores. Cuando el sector es reinstalado debe tenerse cuidado en apretarse las tuercas de manera uniforme. Si no son ajustados de modo correcto, el disco no girará en línea recta. Esto es como los rayos de la rueda en una bicicleta, si no son apretadas uniformemente luego la rueda se bamboleará.

Filtro De Discos Americano
Consta de una serie de discos circulares montados sobre un eje central, el cual se encuentra sobre un tanque. El eje es soportado por dos rodamientos y es conducido por un tornillo sin fin de manera similar a un filtro Oliver. Su velocidad promedia es aproximadamente una revolución en ocho minutos. Una válvula de control automática del mismo tipo como la que ya describió es fijada a uno de apoyos del eje. Cada disco está compuesto de ocho para lo diez sectores. Cada sector uno está cubierto de una bolsa de tela o con otro material adecuado.
Sectores De Un Filtro De Discos
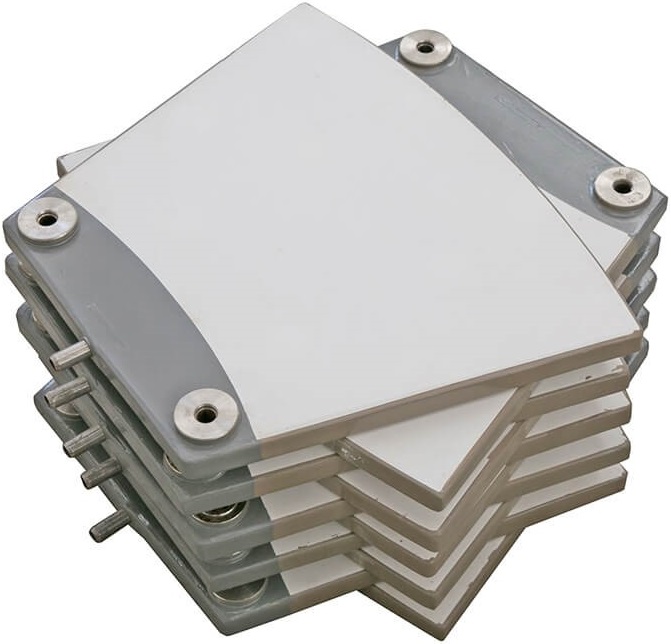 |
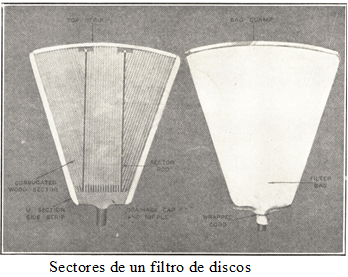 |
Los sectores antiguos eran hechos de madera, con canales o ranuras para el drenaje rápido del agua a través de las bolsas filtrantes. Cada uno es montado con un niple que cabe dentro de un hueco en el eje central comunicándose con el canal de drenaje, y se justa con una herramienta neumática. Unas barras se proyectan del eje central como los rayos de la rueda de una rueda y están tan organizadas de modo que entren dentro del espacio izquierdo entre los bordes de sectores adyacentes. Una abrazadera del marco, diseñada para agarrar las dos esquinas contiguas de los sectores, está en cada barra y asegurada por una tuerca. Así, cuando todas las abrazaderas están en posición correcta y sus tuercas apretados, los sectores son sujetados firmemente en su lugar alrededor del eje en la forma de un disco completo. Una gran ventaja de esta construcción es que una bolsa dañada del filtro puede cambiarse en pocos minutos sin alterar los otros sectores. Cualquier número de discos puede ser montado en el eje.
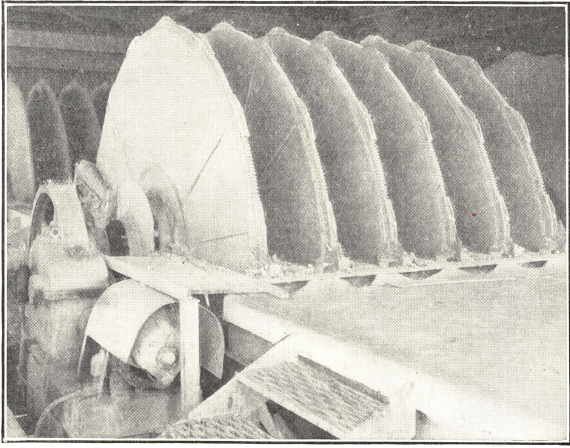
Filtro de Discos Americano
El interior del eje central tiene el mismo número de canales de drenaje longitudinales como haya sectores en un disco, cada uno de los canales se conecta con una válvula automática; Los sectores correspondientes en cada disco drenan en el mismo canal. La válvula automática controla el ciclo de operaciones – la formación del queque (en ambos lados del disco) y el secamiento bajo vacío, y la descarga bajo la presión – como en un filtro del tambor. La remoción del queque es facilitada por rodillos que se conectan con cada lado de la bolsa durante el soplado. El tanque está colocado entre los discos en la descarga lateral a fin de darle al material una caída libre. Ningún mecanismo agitador está instalado. Si se presenta alguna dificultad por asentamiento de partículas pesadas, la pulpa le es bombeada a través del fondo del tanque y rebosa de regreso a la bomba, el nivel se mantiene lo suficientemente rápido para mantener a los sólidos en suspension. Por regla general, sin embargo, el movimiento de los discos provee suficiente agitación.
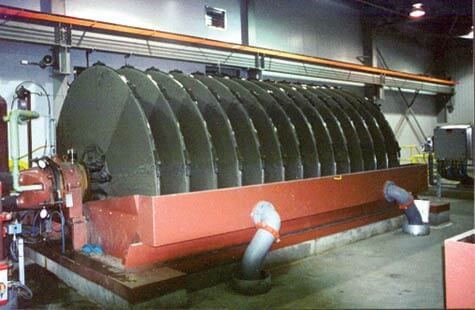
Los filtros americanos son hechos con los siguientes diámetros:
Diámetro |
Área Filtrante – ft² |
4 pies 0 pulgadas |
22 |
6 pies 0 pulgadas |
50 |
8 pies 6 pulgadas |
93 |
12 pies 6 pulgadas |
200 |
Cualquier número de discos puede ser montado en el eje, pero en la práctica el máximo número abastecido rara vez excede el número de pies del diámetro del disco adaptado. Por ejemplo, el máximo número de discos de 8 pies 6 pulgadas que se colocan en un filtro es ocho.
Por esta razón nos quedaremos con el filtro de discos rotativo y lo usaremos como nuestro modelo. Los componentes del filtro comienzan con el punto de alimentación al tanque del filtro, el cual es la porción del filtro a la que el concentrado es bombeado, para permitir el acceso del filtro.
Tendrá un chute como punto de descarga para el concentrado filtrado, y un chute de ingreso para el concentrado húmedo.
Debido a que la rapidez de filtración es a menudo más lenta que la velocidad de la bomba de alimentación, hay una línea de rebose provista para el material que no se filtró y debe ser devuelta a su punto de origen. La alimentación puede venir de un tanque de retención o de un espesador. Si la tasa de sedimentación del concentrado es rápida, el tanque del filtro también puede tener un agitador para mantener los sólidos en suspensión en el líquido.
Los discos Rotatorios, que pueden ser mas de uno, dan vueltas a través de la pulpa. Luego el vacío comienza a participa en el sistema. Un vacío es aplicado a la pulpa a través de los discos rotatorios. El concentrado está atrapado en la superficie del disco mientras el agua es succionada a través de los sectores. Cada disco está hecho de una serie de SECTORES removibles del Filtro.
Sobre estos sectores se filtra el concentrado. Cada sector esta cubierto con un tela hecha de nilón o algodón. Sobre el sector existen canales para asegurar que el vacío ingrese a través de la tela.
Cuando el vacío succiona la pulpa, el agua pasa a través de las aberturas de la tela y el concentrado es retenido sobre la superficie. Luego ser retenido, es dejado caer fuera del sector y es descargado a través de un chute. El proceso es hecho en una forma continua por ciclos. Luego de descargar el concentrado, el sector entra en el tanque con pulpa.
https://www.wikiwand.com/en/Rotary_vacuum-drum_filter
A medida que el vacío (la succión) es aplicado. Esto se llama etapa de levantamiento (en la zona de filtración) porque el vacío en el sector del filtro realmente recoge el concentrado y mantiene el mineral sobre el sector mientras continúe dando vueltas. Cuando el sector que tiene el concentrado es levantado y deja la pulpa entra en el ciclo de secado. Esto es cuando el vacío jala tanto agua como pueda del concentrado.
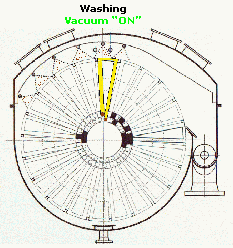
Como el sector del disco termina la última parte de una revolución completa, una cantidad de aire es soplada dentro del sector causando que la tela filtrante se abulte hacia el exterior. Esto remueve el concentrado del sector. El soplado de aire ocurre mientras el sector es sobre el chute de descarga del filtro. El sector luego entra en la pulpa otra vez para empezar otro ciclo de filtración.
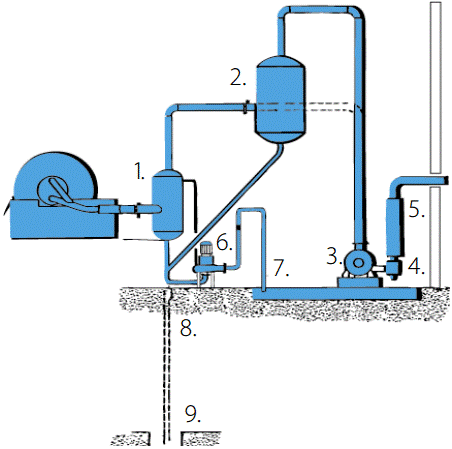
Sistema típico de un filtro a vacío de discos equipado con una bomba para el filtrado y colector de vacío. 1. Colector de vacío. 2. Trampa de humedad (para filtrados especiales). 3. Bomba de vacío. 4. Separador de Liquido. 5. Silenciador. 6. Bomba de filtrado. 7. Drenaje del piso para plantas sin bomba de filtrado. 8. Línea de drenaje desde el tanque de vacío. 9. Sello de agua.
Separacion Solido-Liquido Con Un Filtro De Discos
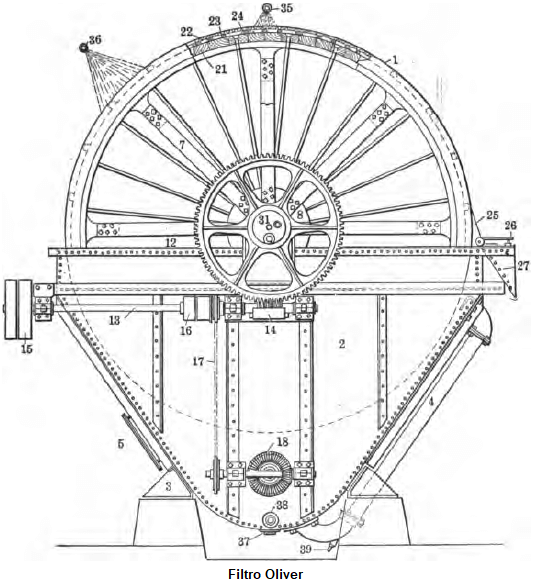
Este filtro es de precio moderado, sus costos operativos son bajos, y es continuo en funcionamiento, y mientras aún no puede ser considerada una solución perfecta del problema de filtración parece tener los elementos de más utilidad permanente que cualquier otro dispositivo en el presente.

Sus principales desventajas son su pequeña capacidad de lavado, necesitando uno o más lavados de decantación antes de la filtración, y las dificultades mecánicas para mantener la pulpa mezclada y agitada en los casos donde hay una mayor proporción de material granular o arenoso. Su mejor rendimiento es cuando es utilizado como un separador solido-liquido después de que varias decantaciones han sido efectuadas para separar una solución rica, y cuando el material que lo alimentó se acerca a la definición de una pulpa verdadera.
Con esto, al igual que con todos los demás filtros al vacío, una pulpa espesa es esencial para la buena operación, para asegurar la homogeneidad de la pulpa en el tanque y también para obtener una alta capacidad por unidad.
El Filtro de Discos no es comparativamente nuevo, y parece estar haciendo trabajo satisfactorio donde se usa.
Otro tipo de filtro es representado por el Kelly, el Sweetland, y el filtro Burt. El principio básico de éstos es instalar un número de hojas filtrantes verticales en un receptáculo cerrado y haciendo ingresar la pulpa apretadamente por presión mecánica en tal receptáculo, con el resultado de formar queques en las hojas y expeler un licor claro en una tubería de drenaje exterior.
Los métodos de descarga varían. En el Kelly las hojas son colocadas en un carro antes de descargarlos. En el Sweetland las hojas se quedan sin mover y la mitad más baja es removida, mientras en el Burt el queque es primero soplado completamente y luego el material remanente es removido, el ultimo es colocado en un ángulo pronunciado, el queque se desliza fuera tan pronto como una compuerta es removida.
El filtro Burt es diferente a otros. Consta de un tubo horizontal giratorio algo como un molino, y tiene un forro completo de filtro material. La pulpa es alimentada bajo presión mecánica y un queque se forma arriba en forma de un forro uniforme dentro del tubo y con 1 a 4 o 5 pulgadas en el espesor. Cuando el suministro de pulpa es recortado, la presión es mantenida con aire comprimido a fin de que la filtración puede ser conllevada al final y no es necesario remover un exceso de pulpa. Para la descarga, un extremo del cilindro es removido y el movimiento giratorio es reiniciado, el queque automáticamente cae y se descarga sobre una canaleta.
Arreglo De Un Espedador Con Un Filtro De Vacio De Discos
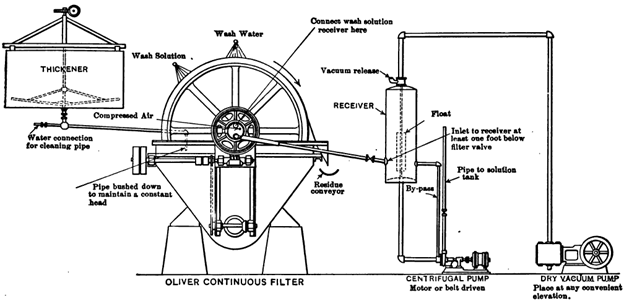
Bomba de vacío, tanque colector para el filtrado, espesador, agua de lavado
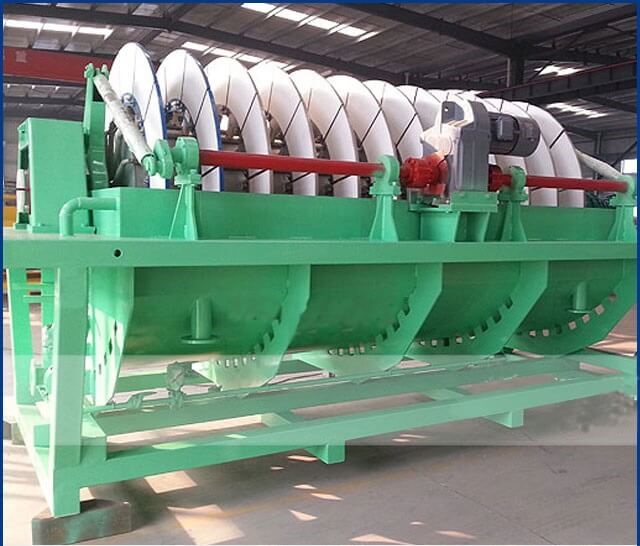
Filtro De Discos Ceramicos De Laboratorio